How to Properly Maintain your Lubrication System
Buildup… Contamination… What Happened?
Six months after your Digilube system was installed, you start to notice the performance of your conveyor equipment declining. You see there is buildup on the rail, chains and trolleys resulting in dust and dirt collecting on the rail. You have oil dripping on the production floor. What is the cause of this mess?
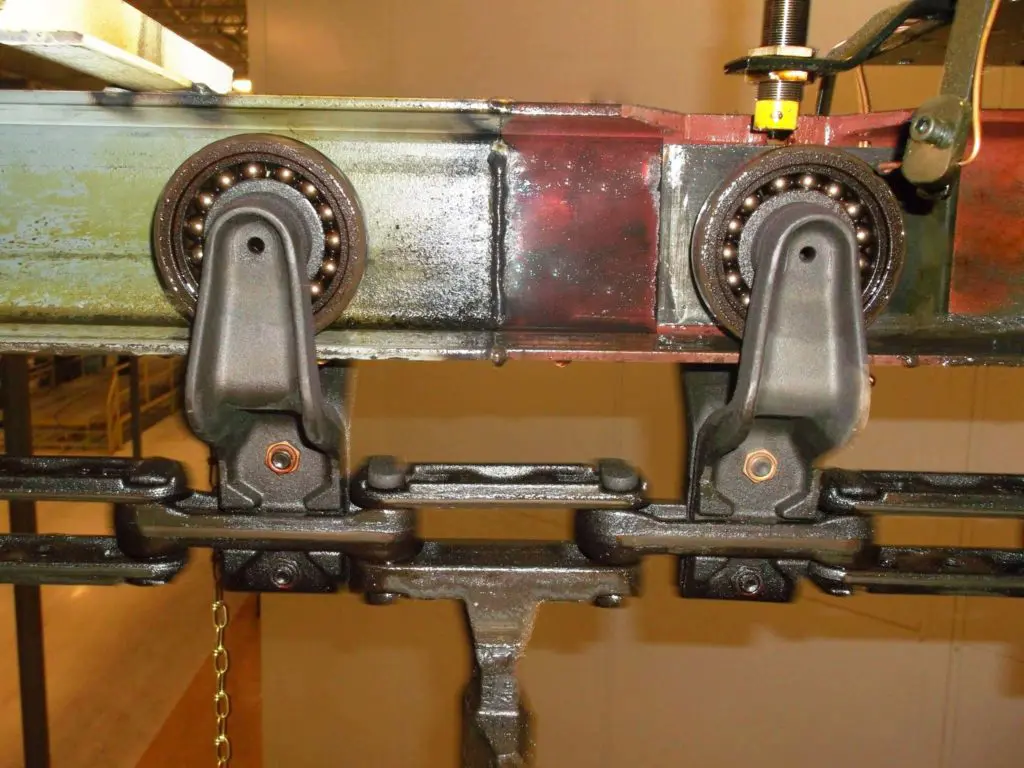
While Lubrication is the key to chain longevity, there are several factors that can cause problems if a system is not lubricated and maintained properly:
- Over Lubrication
- Misaligned Equipment
Sensors
The first thing to do is take a look at the sensors to see how they are functioning. It’s very important for the sensors to communicate to the head controller at what intervals the pins need to be lubricated. If they are out of adjustment, this causes shots of lubricant to miss the pins, resulting in drippage.
Dispensing Tubes
If the dispensing tubes are not pointed at the bearing and calibrated properly, this causes build up on the rail. The lubricant hits the outer race instead of the bearing, resulting in lubricant drips causing build-up from dust and debris. Constant vibrations over time can also mess with the accuracy of the dispensing tubes.
Lubrication Cycle
If the sensors are functioning properly and the dispensing tubes are calibrated properly, then a change in the lubrication cycle might be necessary. Sit back and think, has something changed in your production? Perhaps the chains are not staying in the ovens as long, or the load on the chains has decreased.
Below you can see several examples of poorly maintained rails, chains and trolleys.
Dust and Debris collected from lack of cleaning rail An Over Lubricated System dripping on shop floor Rust
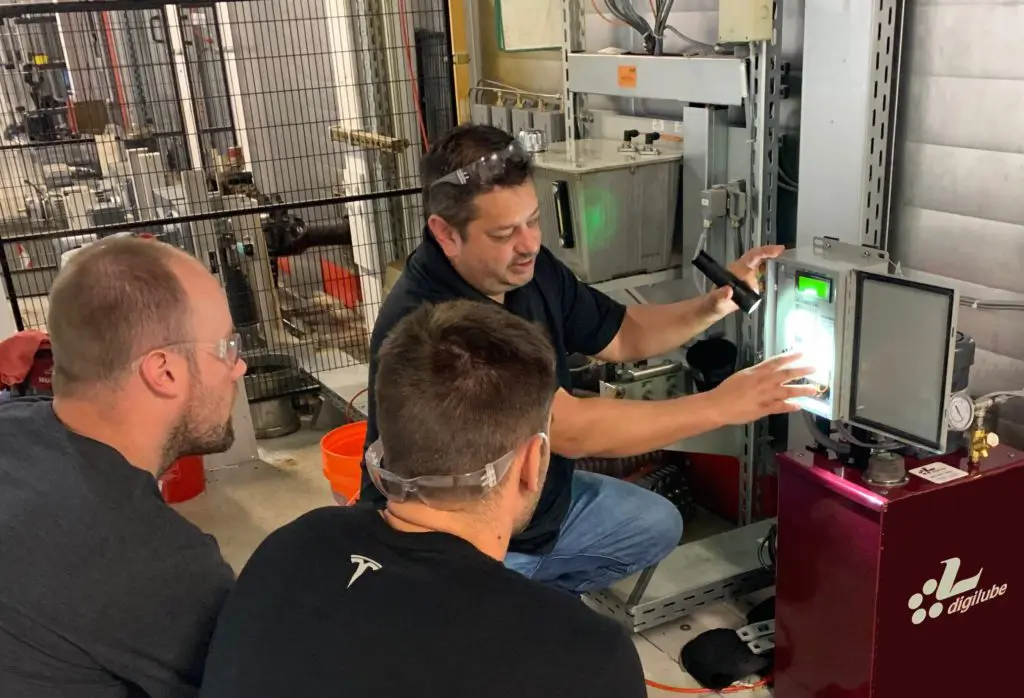
Solutions
Quarterly Maintenance
Let us take the stress out of conveyor maintenance. We offer service contracts at the customer’s request, in which our highly trained field service technicians will give the conveyor chain a thorough inspection. Our top priority is ensuring the lubrication equipment and it’s components is working in optimal working condition. Overall, this will elongate the life of the conveyor system, as well as the chain iteself.
Precise Lubrication
The convenience of the DL-5003 Head Controller takes the guesswork out of lubrication. This controller is desgined to ensure your equipment is precisly lubricating the critical bearing points of the conveyor chain. During installations, maintenance managers are trained on the head controller settings needed to fit their schedule of operation.
Cleaning Recommendations
We recommend checking the photo sensors and alignment of dispensing tubes once a month, depending on the facility’s environment. We offer several types of Beam Cleaners that attach to the trolleys, cleaning the chains and rails on days production is down. Keeping the wear area cleared of buildup allows lubricant runs at max wear points. We recommend the beam cleaners are run every 3 months.